GBMP Launches Comprehensive Lean Training Tool, “Seeing the Invisible”
One of the most essential tools for a strategic Lean transformation is to engage the entire workforce in Total Productive Maintenance. And while there are many good texts that describe Total Productive Maintenance (TPM) theory and strategy, little has been provided to stimulate the thinking and passion of the people who do the work. That is, until now.
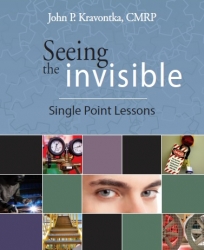
Boston, MA, July 25, 2013 --(PR.com)-- Regrettably the implementation of TPM has been limited by the same traditional paradigms that inhibit effective Lean transformation. It is a fact that many factories struggle with basic PM, their maintenance staffs stretched to the limit. With inadequate resources to assure a stable operating environment, many factories operate today in a run to failure mode, moving from one crisis to another. TPM seeks to align all company resources in a manner that continuously identifies and reduces the losses caused by equipment failure - the word failure referring both to equipment that is actually stopped and also equipment that may be running but is not functioning properly. In the absence of TPM, the latter category is especially invisible.
GBMP is well known for its extensive suite of lean training products including 30+ DVDs, books and best practice training games. Their newest lean training tool, "Seeing the Invisible" is a comprehensive manual providing many examples of quick and often easy solutions that will nurture employee expertise and creativity, and encourage practice and sharing within an organization. “Seeing the Invisible – Single Point Lessons” provides readers with an innovative and invaluable approach to equipment maintenance that builds productive capability, customer value, employee safety, engagement, and development.
The concept of shared responsibility for equipment reliability, Total Productive Maintenance provides an as yet undiscovered opportunity in many status quo plants, where problems are invisible, hidden by excess resources and cost. The aim of “Seeing the Invisible – Single Point Lessons” is to make invisible visible; to provide an approach to equipment maintenance that builds productive capability and customer value through engagement and development of every employee, from machine operators to maintenance technicians to plant managers. TPM is, in the words of its creator Seiji Nakajima, “an activity carried out by all employees through small group activities.” In this sense, TPM shares a requirement for culture shift that is very much like that in organizations seeking a Lean transformation. As with any other aspect of continuous improvement, TPM strives for an all-inclusive involvement creating a professional challenge for production employees as well as maintenance personnel to maintain perfect operating conditions for equipment every minute of every day.
The goal of “Seeing the Invisible” is to inspire readers to begin to create and circulate their own Single Point Lessons – to capture and categorize the good ideas and best practices, using words and pictures, and disseminate them at lightning speed, eliminating the need to re-invent the wheel. Readers of the manual can use the ideas and best practices in the book to teach the concepts and employees can adapt these concepts to their own facility, processes, and equipment. Regardless of the size or age of an organization, regardless of the number of employees or types of equipment, regardless of the nature of the business, be it a manufacturing or healthcare facility, industrial plant, university or school system, office, warehouse or laboratory, it is our belief that the examples in the book, these Single Point Lessons, will help foster the concept of shared responsibility for equipment reliability, change ideas at your facility, and result in improved safety, quality, lead times and profit.
The work done by the author John Kravontka and his associates at Fuss & O’Neill is essential and foundational to Toyota Production Systems (TPS) success and World Class operational excellence, and, according to Bruce Hamilton, President of GBMP, “everyone is very excited at the visibility created in this manual by John’s many single point lessons. “Seeing The Invisible” will energize your strategic Lean transformation by engaging your entire workforce, which is after all the aim of Total Productive Maintenance. TPM is learned by doing; this manual is a guideline for doers. We hope the lessons contained in this manual will both inform and inspire you to copy first, but then to create and share your own single point lessons.”
The book will be available beginning Monday, July 29th at on shopgbmp.org
About GBMP, Inc: Based at the University of Massachusetts, Boston, GBMP is a non-profit corporation that has worked with hundreds of companies, providing education and coaching resulting in millions in cost savings and increased sales. Each year GBMP trains over 7000 people on Continuous Improvement principles in customized, on-site classroom and shop-floor training sessions and educates thousands more in public workshops, on plant tours, at its annual continuous improvement conference and through its line of award-winning Lean training products, including the #1 Selling Lean Training DVD in the world, Toast Kaizen. GBMP is an educational partner of The Shingo Prize for Operational Excellence in the Northeastern Region of the United States and three-time recipient of the Research Prize. Visit gbmp.org, shopgbmp.org or neshingoprize.org for more information.
GBMP is well known for its extensive suite of lean training products including 30+ DVDs, books and best practice training games. Their newest lean training tool, "Seeing the Invisible" is a comprehensive manual providing many examples of quick and often easy solutions that will nurture employee expertise and creativity, and encourage practice and sharing within an organization. “Seeing the Invisible – Single Point Lessons” provides readers with an innovative and invaluable approach to equipment maintenance that builds productive capability, customer value, employee safety, engagement, and development.
The concept of shared responsibility for equipment reliability, Total Productive Maintenance provides an as yet undiscovered opportunity in many status quo plants, where problems are invisible, hidden by excess resources and cost. The aim of “Seeing the Invisible – Single Point Lessons” is to make invisible visible; to provide an approach to equipment maintenance that builds productive capability and customer value through engagement and development of every employee, from machine operators to maintenance technicians to plant managers. TPM is, in the words of its creator Seiji Nakajima, “an activity carried out by all employees through small group activities.” In this sense, TPM shares a requirement for culture shift that is very much like that in organizations seeking a Lean transformation. As with any other aspect of continuous improvement, TPM strives for an all-inclusive involvement creating a professional challenge for production employees as well as maintenance personnel to maintain perfect operating conditions for equipment every minute of every day.
The goal of “Seeing the Invisible” is to inspire readers to begin to create and circulate their own Single Point Lessons – to capture and categorize the good ideas and best practices, using words and pictures, and disseminate them at lightning speed, eliminating the need to re-invent the wheel. Readers of the manual can use the ideas and best practices in the book to teach the concepts and employees can adapt these concepts to their own facility, processes, and equipment. Regardless of the size or age of an organization, regardless of the number of employees or types of equipment, regardless of the nature of the business, be it a manufacturing or healthcare facility, industrial plant, university or school system, office, warehouse or laboratory, it is our belief that the examples in the book, these Single Point Lessons, will help foster the concept of shared responsibility for equipment reliability, change ideas at your facility, and result in improved safety, quality, lead times and profit.
The work done by the author John Kravontka and his associates at Fuss & O’Neill is essential and foundational to Toyota Production Systems (TPS) success and World Class operational excellence, and, according to Bruce Hamilton, President of GBMP, “everyone is very excited at the visibility created in this manual by John’s many single point lessons. “Seeing The Invisible” will energize your strategic Lean transformation by engaging your entire workforce, which is after all the aim of Total Productive Maintenance. TPM is learned by doing; this manual is a guideline for doers. We hope the lessons contained in this manual will both inform and inspire you to copy first, but then to create and share your own single point lessons.”
The book will be available beginning Monday, July 29th at on shopgbmp.org
About GBMP, Inc: Based at the University of Massachusetts, Boston, GBMP is a non-profit corporation that has worked with hundreds of companies, providing education and coaching resulting in millions in cost savings and increased sales. Each year GBMP trains over 7000 people on Continuous Improvement principles in customized, on-site classroom and shop-floor training sessions and educates thousands more in public workshops, on plant tours, at its annual continuous improvement conference and through its line of award-winning Lean training products, including the #1 Selling Lean Training DVD in the world, Toast Kaizen. GBMP is an educational partner of The Shingo Prize for Operational Excellence in the Northeastern Region of the United States and three-time recipient of the Research Prize. Visit gbmp.org, shopgbmp.org or neshingoprize.org for more information.
Contact
GBMP
Lela Glikes
617-287-7630
www.gbmp.org
Lela Glikes
617-287-7630
www.gbmp.org

Categories